Process Functional Modeling (PFM) is an analytical tool that helps us to learn the process through modeling different operations of the process, solving problems, and defining ways to improve to any process. PFM is built to make better strategic and tactical decisions in identifying opportunities for improvement and implementing solutions in complex processes in an organization.
This help article describes a step by step instructions on how a problem solver can effectively use the process functional modeling method to better identify how the problem can be caused and which process operation is responsible for it.
First, let’s take care of some definitions.
Glossary & Definitions
Process
A process is a set of sequential actions which convert available resources into a desired product. In other words, a process is a way to increase the value of the available resources.
Process operation
As mentioned above, a process consists of a number of sequential operations. An operation is performed by a system and can be classified into 4 different types.
- Productive – an operation that results in irreversible changes in an object. Productive operation increases the value of the final product.
- Providing – an operation that results in temporary changes. Providing operation increases the cost of the process’s final product but never adds value.
- Corrective – an operation that exists due to improper performance of productive operations and existing providing operations. A corrective operation may add some value to the product as a complimentary of the productive operation due to a flaw in the productive operation itself.
- Metrology – an operation that results in no changes and no value added to the product. Metrology operations exist due to flaws in productive operations and the existence of providing operations.
Operation ranks
Every operation in the process has certain functional and problematic ranks. As we will show below, the platform calculates these ranks automatically when we define a functional model for an operation. Once these ranks are available, the functional/problematic ratio is also calculated and presented to us.
- Functional rank – is a measure of the operation’s functional level. This rank alone does not mean much within the context of the whole process model. However, it does add a lot of information in conjunction with problematic rank.
- Problematic rank – is a measure of the operation’s problematic level. This rank alone does not mean much within the context of the whole process model. However, it does add a lot of information in conjunction with functional rank.
- Functional/Problematic Ratio – a measure of how well the operation is performing, or how efficient the operation is. Anything under 2 is considered low-efficiency operations.
Using Process Functional Model
In this article, we will not dig too much into the “why” to use functional modeling, when is it useful and what are the use cases. For that, we have a number of blog articles that we welcome you to read. Here, we will concentrate on the step-by-step instructions and mechanism of how to use the tool.
First, we assume that you already know how to start using a new tool. For more information about that visit Creative Tools article. Process Functional Model is one of the available tools in the PRIZ Innovation Platform.
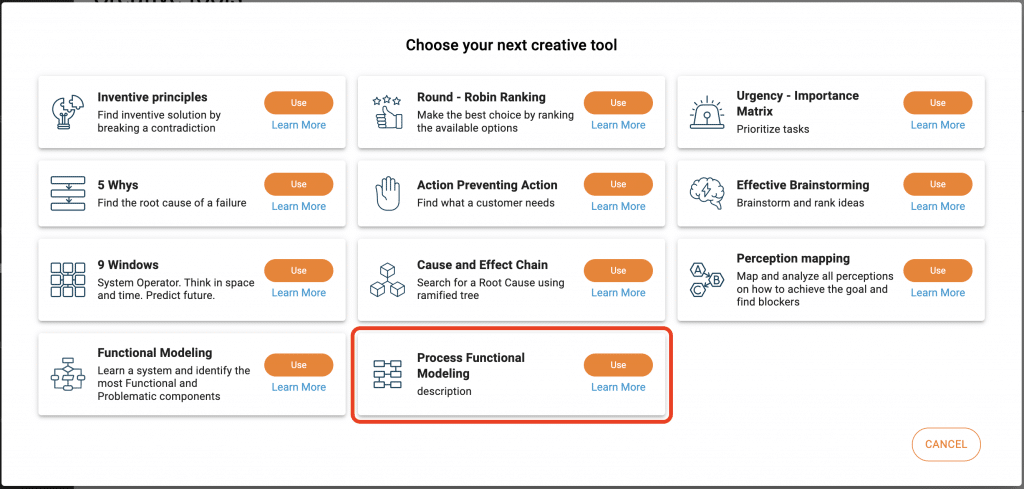
Once the tool instance is created, you will be redirected to the tool itself.
Similar to many other tools, Process Functional Modeling has a number of sections:
- System – a free-form description of a system that you are planning to analyze
- Model – where you will build the actual model
- Summary – this is where you will have a nicely organized summary of the model you created with the relevant suggestions for your process improvements
- Conclusions – free-form description of any conclusions that came out of the analysis
System
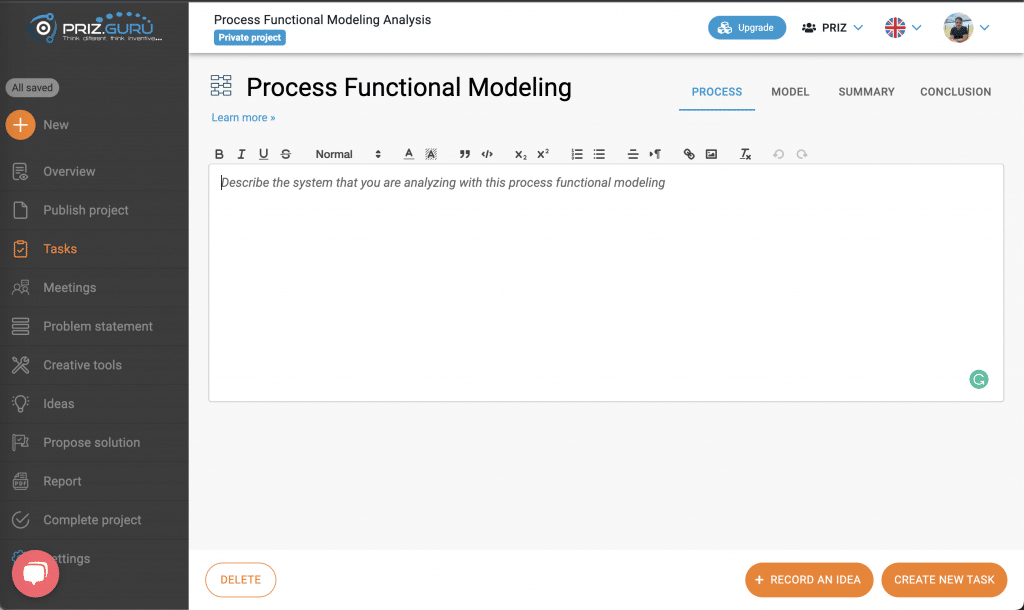
As shown in the screenshot, the system tab has a single, free-form, rich text editor field. This field accepts most of the basic formatting as well as images.
The purpose of the systems field is to allow you to describe the details of the system (or in this case, the process) that you are analyzing and building the function model for. It’s proven that documenting the system in your own words and having this description in front of your eyes during the analysis, help the innovator to build a better model. Also, while you and your team describe the system, it forces you to think and rethink the details that you would miss otherwise.
On another note, it is important to understand that you don’t have to create the perfect system description before moving to the modeling step. You can always come back here and add more information at any point during the process. In fact, this is what usually happens and it is normal. A team starts working on modeling the system and comes across or remembers things that have been missed initially.
Model
Here, in the model tab, you will spend the majority of your time building the process functional model. This is the most important step in the tool.
The first time after the tool is prepared for use, it offers a default empty state.
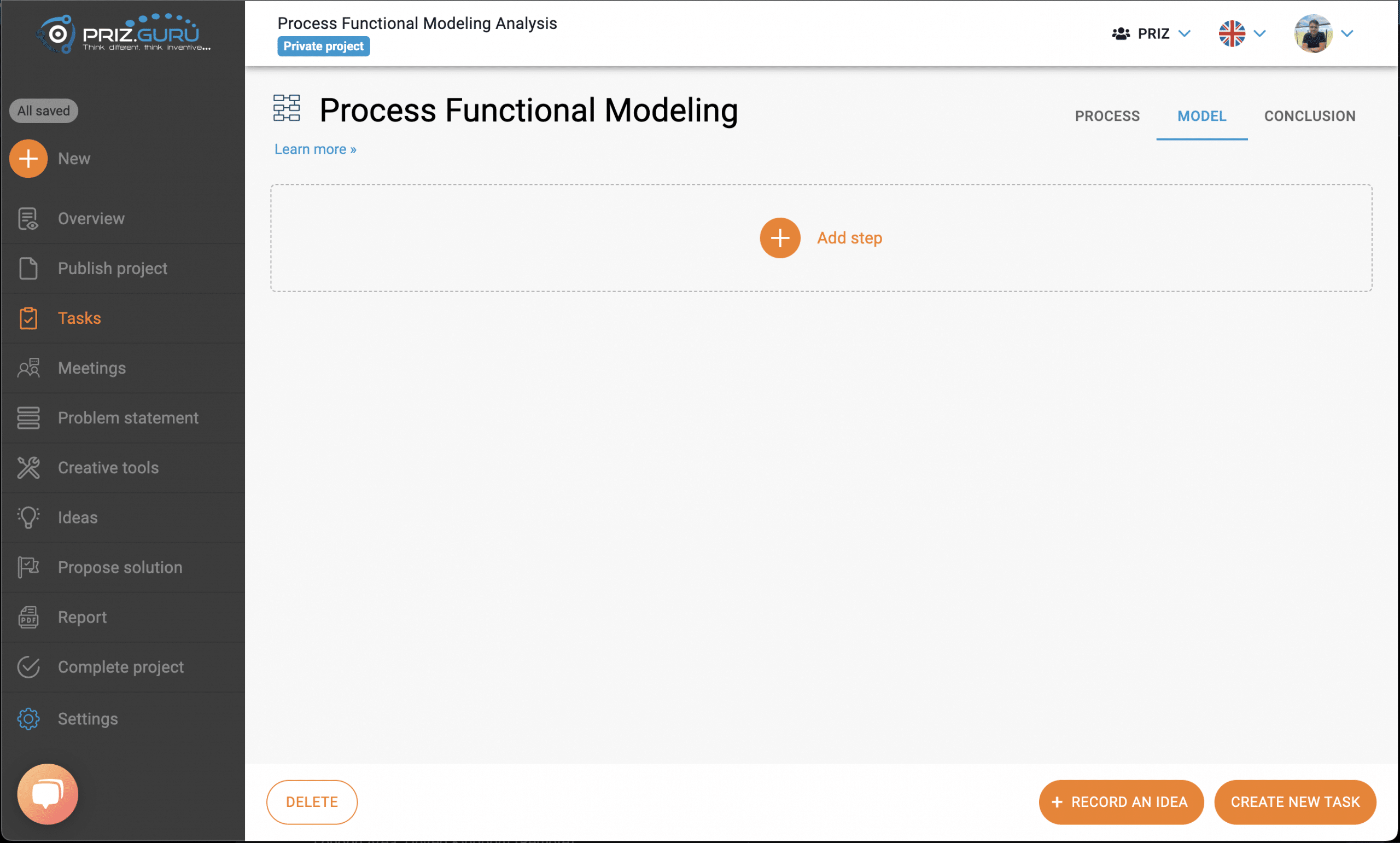
As we can observe, the only useful thing we can do here in order to continue is to add the first step. Remember? The process is a series of sequential operations (or steps). Go ahead and click on Add step button. This will create your first operation in its default state.
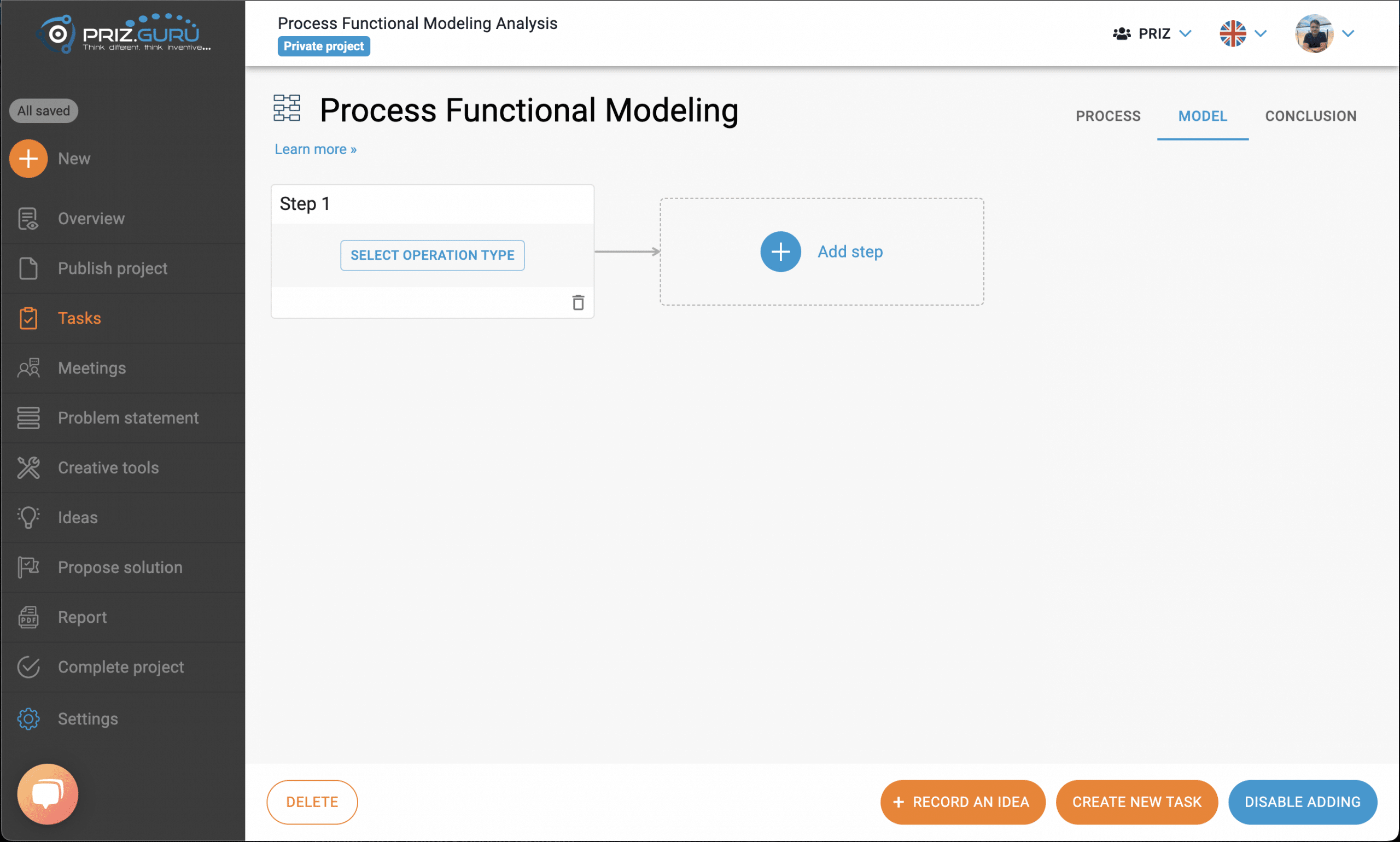
The created operation will automatically have a default title set for it. We will discuss the details of how to change it. At this stage the interface allows you to continue with the chain of operations by clicking “Add step” as many times as needed. So, let’s create a few and explore the options and controls.
Canvas & controls
Now let’s go over some of the controls available for you on the work canvas of PFM.
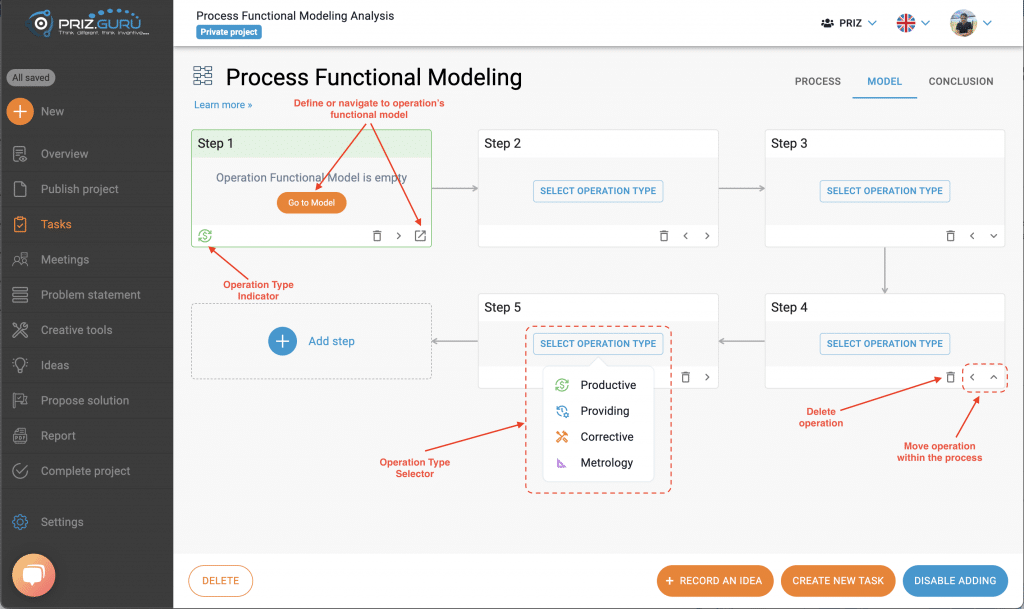
Here, we created several operations to show all the different controls available on every operation.
Selecting Operation Type
In operation Step 5, we are showing the initial state of created operation. As the rules go, we need to choose the type of operation first. For that reason, initially, that is the only thing you can do with the operation: Select operation type. Once clicked, you’ll be able to choose the type.
The operations with the already selected type will have an indicator of that type (i.e. Step 1 lower left corner). Clicking on the indicator will allow you to change the type at any point in time.
Deleting an operation
You are able to delete any of the operations if needed. Every operation has a `trash can` button in the lower right corner. Clicking on it will delete the operation.
In case you delete one in the middle of a defined process, the remaining will be relinked to keep the continuity of the process.
Moving an operation
Any operation can be moved within the process (reorder the operations). You will find the controls to do so at the lower right corner of the operation container.
Defining the Functional Model of an operation
After you selected a type of operation, you can now define the functional model of that operation. This is the second most important step in the analysis, as it provides information about how well the operation is performing. We’ll expand a bit more about it later.
Step 1 in the screenshot has both options to start working on the functional model of the operations. In case it was not yet defined, you will have a big Go to Model button that will navigate you to the Functional Modeling tool to do the work.
Another option is the small link button which will lead you to the same linked functional model.
Building the operation Functional Model
Here, we will not go into the details of how to use the Functional Modeling tool. You can read about it in the dedicated article. However, there is a slight difference when you are using the functional modeling linked to PFM.
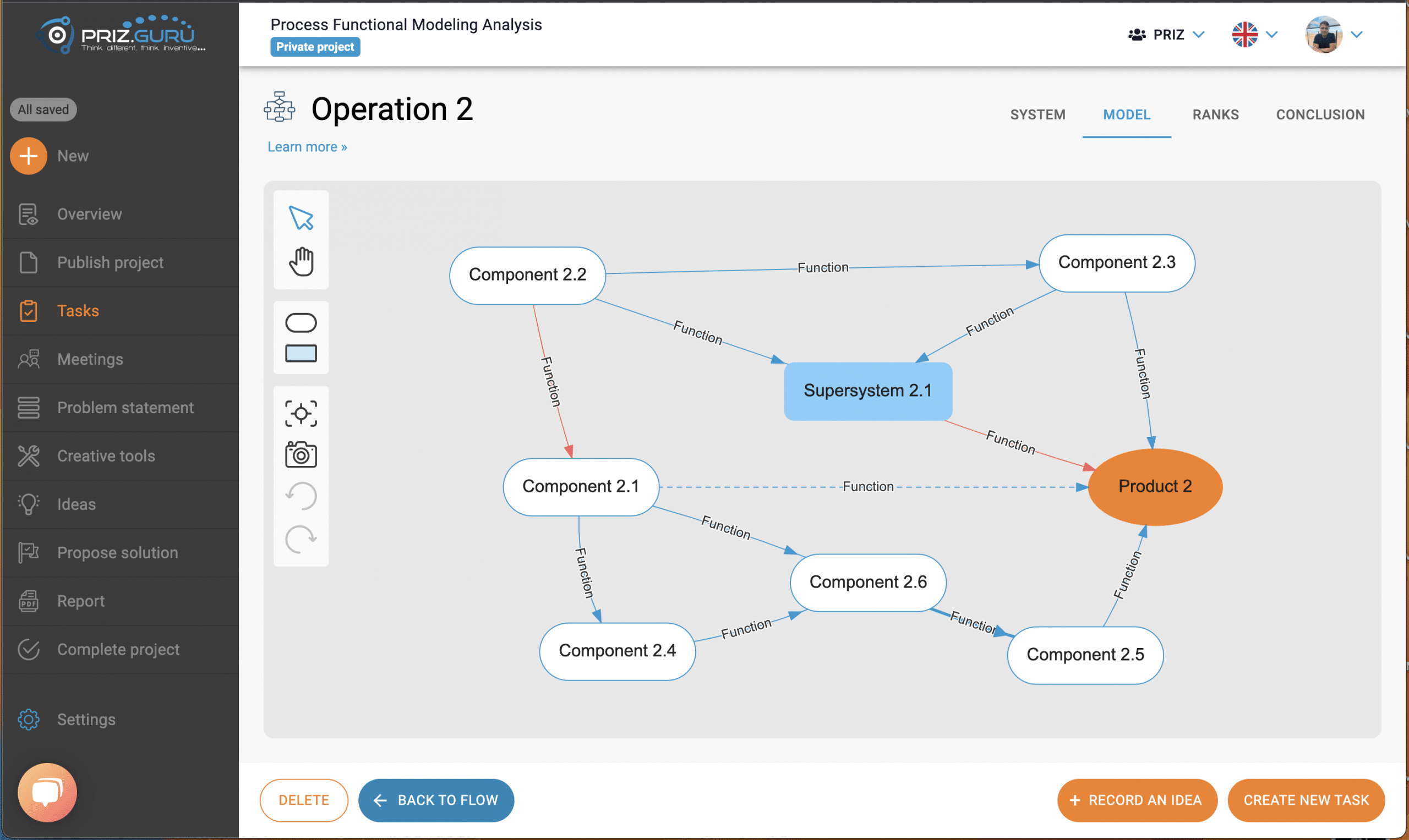
In this case, you will have a BACK TO FLOW button that will take you back to the process analysis. Everything else is just the same old System Functional Model.
Viewing and understanding the results
Let’s now assume that you finished defining the functional models for all important operations in the process. The representation of the process will look slightly different and will provide the details to make your strategic decisions.
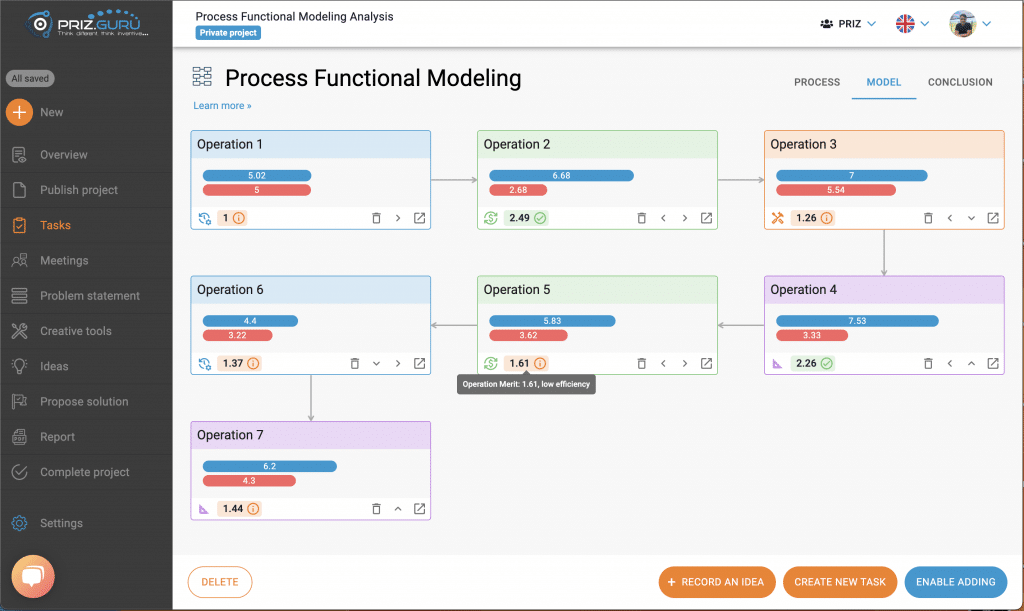
As shown in above, at this point, all the operations have all the collected information:
Operations type – every operation is color-coded based on the operation type, in addition to the type indicator that we talked about before.
Functional & Problematic Ranks – for every operation the platform calculated the overall functional and problematic ranks of the entire operation. Functional rank is represented with a blue bar, while problematic rank is in red. These ranks are extremely important to understand the efficiency of an operation.
Operation efficiency – the small number at the bottom of every operation indicates the efficiency of the operation. Anything under 2 means low efficiency.
Note: this is where we need to focus our efforts in order to improve the process.
Summary
As mentioned above, this tab will have a nicely organized summary of the model you created with the relevant suggestions for your process improvements.
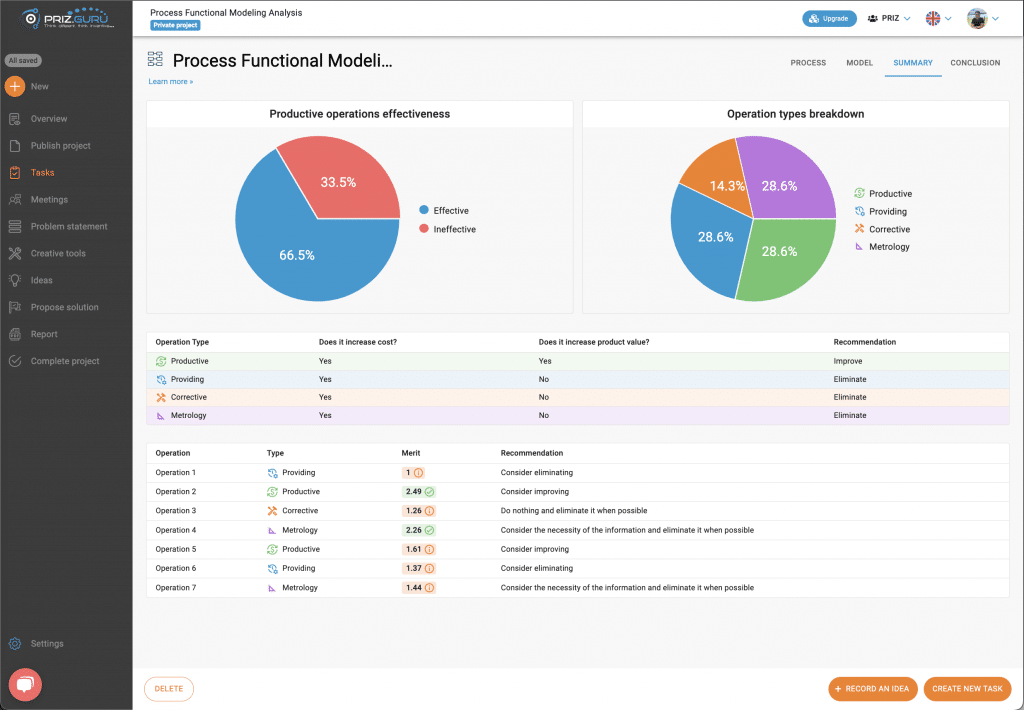
The most important piece of information that the summary provides is how effective the process is overall. Also, it will provide suggestions about where should we focus our attention and what operation we need to invest in.
Conclusion
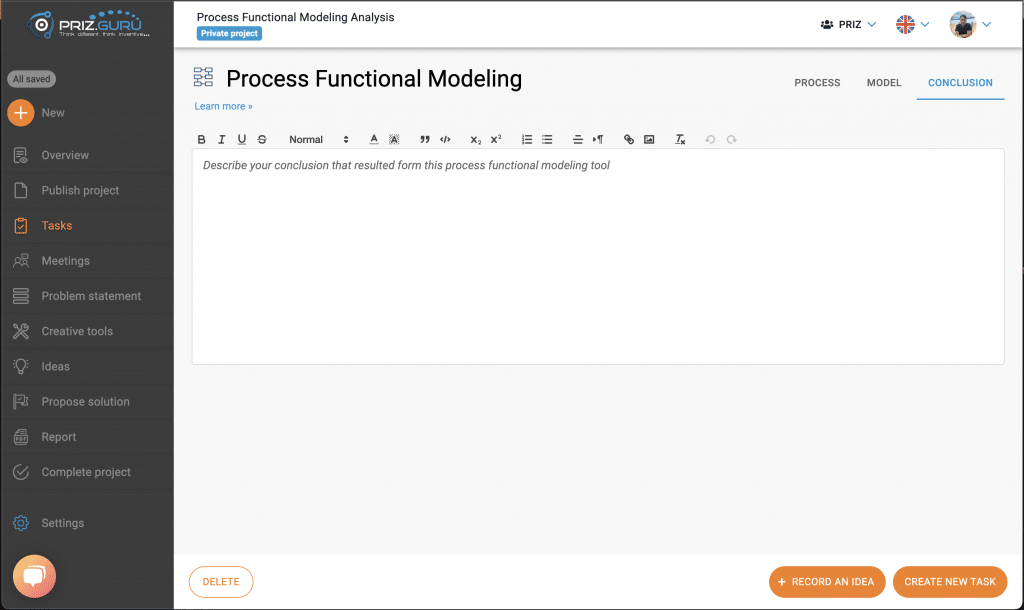
The conclusion tab is the place where you can document any conclusions that you have as a result of process functional model analysis. This is a free-form rich text editor. Similar to the system tab, you are welcome to have any information you feel is useful for you, your team, and your leadership. The conclusion will also be included in the final report with anything else related to your work with this tool.
Tool controls & final notes
Like any other tool, PFM also has controls at the bottom of the page.

These controls are always visible while you are working on any tool.
Delete button allows you to delete one particular use (instance) of a tool, in case you decided that you don’t need it.
Record an Idea button allows you to record an idea at a project level at any point in time. These ideas are collected in ideas manager.
Create New Task button allows you to create a new task without leaving a tool. Just imagine that, while working on a tool, you and your team decided that there is something that you need to do. This is how you would record that task.
Enable/Disable Adding button toggles the completion of the process. It will basically hide the ability to add more steps in the process. This is purely for visual convenience.
That’s it! Happy innovations and process improvements.
Contact us with any questions.